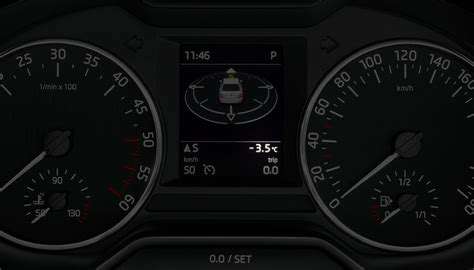
Understanding the Absence of Automation
Level 0, in this context, signifies a complete lack of automation in a process or system. This means that every aspect of the task, from initiation to completion, relies entirely on human intervention. This approach, while potentially offering greater control and flexibility in certain situations, often comes with increased costs and time commitments. Recognizing this crucial difference is important for effective planning and resource allocation.
Manual processes can be prone to human error and inconsistencies, leading to variations in output quality and potentially impacting overall efficiency. Thorough oversight and careful monitoring are therefore essential to mitigate these risks.
Challenges of Manual Operations
Operating without automation presents a range of challenges. Foremost amongst these is the significant time investment required. Tasks that could be automated in a matter of minutes may take hours or even days to complete manually. This extended timeframe can impact project timelines and overall productivity. Furthermore, the potential for errors is dramatically increased in manual operations, requiring extensive quality assurance checks to ensure accuracy.
Resource Allocation and Management
Implementing a Level 0 approach demands careful allocation of resources. Human capital, including expertise, training, and personnel, becomes a critical factor. The cost of human labor must be considered alongside the potential for delays and errors. Effective management of these resources is crucial to maintaining a functional workflow in the absence of automation.
Careful planning and scheduling are also essential to avoid bottlenecks and ensure that tasks are completed within acceptable timelines. This often requires a high degree of coordination and communication amongst team members.
Potential Benefits of Manual Processes
While manual processes generally face drawbacks in terms of speed and efficiency, they can offer certain advantages. In situations requiring highly customized or intricate work, human expertise can often deliver results that automated systems are unable to replicate. Manual processes can be invaluable for intricate tasks that demand a high degree of precision and nuanced judgment. Creative problem-solving and adaptability are also strengths of a manual approach.
Alternative Approaches and Considerations
Considering the limitations of a Level 0 approach, it's crucial to explore alternative strategies to improve efficiency and reduce reliance on manual processes. This can involve evaluating potential automation opportunities, exploring the feasibility of process optimization, and considering the cost-benefit analysis of various solutions.
Understanding the specific requirements of the task is vital in determining if a manual approach is truly the best solution or if automation or other optimization techniques offer a more effective and efficient pathway.
Level 2: Partial Automation
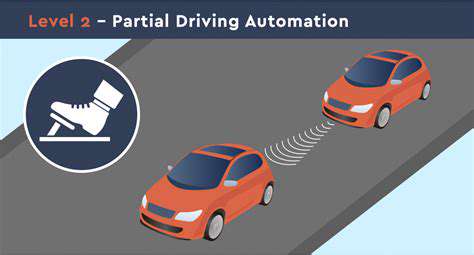
Partial Automation in Manufacturing
Partial automation in manufacturing involves the integration of automated systems into existing manual processes. This approach offers a significant improvement over purely manual operations, increasing efficiency and productivity while still retaining some human oversight. This strategy allows companies to gradually transition to more automated systems, mitigating the risk and cost associated with a complete overhaul. By automating specific tasks, such as material handling or quality control, manufacturers can streamline their workflows and improve output.
The benefits of partial automation extend beyond increased productivity. Reduced labor costs and improved product quality are frequently observed results. This approach allows companies to maintain control over the production process while reaping the rewards of automation.
Types of Automated Systems
Various automated systems can be incorporated into existing production lines. These systems often include robotic arms for material handling, automated guided vehicles (AGVs) for transportation, and automated inspection systems for quality control. The selection of appropriate systems depends heavily on the specific needs and production process of each company. Careful consideration of the tasks to be automated and the available resources is crucial for a successful implementation.
Choosing the right automation technologies requires a deep understanding of the existing infrastructure and the desired outcomes. A thorough analysis of current processes and future goals is essential to ensure that the implemented automation is effective and cost-efficient.
Implementation Strategies
Implementing partial automation requires a well-defined strategy. This strategy should outline the specific tasks to be automated, the required equipment, and the necessary training for personnel. Careful planning and execution are paramount to a successful implementation. This approach allows for a gradual integration of automation, reducing risk and maximizing return on investment.
Phased implementation is often the most effective approach. Starting with a pilot project or a small section of the production line allows for testing and refinement before expanding the automation to other areas. This approach also offers a valuable opportunity to evaluate the long-term effectiveness of the automation system.
Cost-Benefit Analysis
A comprehensive cost-benefit analysis is crucial for determining the feasibility and profitability of partial automation. This analysis should consider the initial investment in equipment, the ongoing maintenance costs, and the potential for increased revenue. It is essential to factor in the potential return on investment over a specific timeframe to ensure the project's financial viability.
A thorough assessment of the long-term impact on labor costs and production efficiency is also critical. Careful consideration of these factors will contribute to a more accurate and reliable cost-benefit analysis.
Maintenance and Support
Maintaining and supporting automated systems is essential for their continued operation and effectiveness. A robust maintenance schedule and access to qualified technicians are critical to minimizing downtime and maximizing system uptime. This support is vital for ensuring the efficient and reliable operation of the automation system. Regular maintenance can also help to prevent costly repairs and ensure the system's longevity.
Training personnel on the operation and maintenance of the new automated systems is also important. This ensures that the workforce is equipped to handle any issues that may arise and maintain the system's optimal performance.
Future Trends
The future of partial automation in manufacturing is promising. Technological advancements will likely lead to more sophisticated and integrated automated systems. This trend will likely lead to even greater efficiency and productivity gains. Further development in areas such as artificial intelligence and machine learning will likely play a significant role in the future of partial automation.
The integration of data analytics and predictive maintenance will optimize operational efficiency and reduce maintenance costs. These advancements will enable more precise and proactive management of automated systems, leading to significant improvements in overall production.
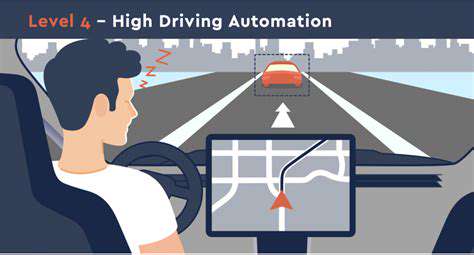