Aluminum Alloys: The Perfect Balance of Lightness and Strength
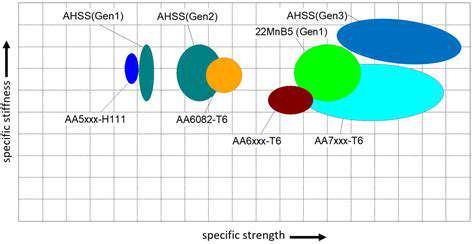
The Science Behind Aluminum Alloy Composition
When we examine modern metallurgy, aluminum alloys stand out as remarkable examples of material engineering. These aren't simple mixtures - they're carefully crafted combinations where each added element serves a specific purpose. The magic happens when copper, magnesium, silicon or zinc atoms integrate with aluminum's crystalline structure, creating materials with properties far surpassing pure aluminum.
Consider aerospace applications where every gram counts. Here, aluminum-zinc alloys (like the 7000 series) demonstrate incredible strength-to-weight ratios. Meanwhile, in marine environments, aluminum-magnesium alloys shine with their superior corrosion resistance. This versatility explains why aluminum alloys have become indispensable across multiple industries.
Lightweighting: Transforming Transportation Industries
The transportation sector has undergone a silent revolution thanks to aluminum alloys. Modern vehicles now incorporate these materials in everything from engine blocks to entire body panels. The results speak for themselves:
- Passenger cars: 40% lighter doors without compromising safety
- Trucks: 300kg weight reduction per vehicle translates to 1,500L annual fuel savings
- Trains: Aluminum-bodied carriages reduce energy consumption by 15-20%
In aviation, aluminum alloys enabled the commercial jet age. The Boeing 787 Dreamliner uses advanced aluminum-lithium alloys that are 10% lighter and 10% stiffer than conventional alloys, contributing to its legendary fuel efficiency.
Manufacturing: Where Science Meets Craftsmanship
Creating high-performance aluminum components requires sophisticated manufacturing techniques. Extrusion processes, for instance, can produce complex profiles with tolerances within 0.1mm. Modern foundries now use computer-controlled die casting that achieves near-net shapes, minimizing material waste.
The real artistry comes in heat treatment. Precise temperature control during aging can triple an alloy's tensile strength. Aerospace manufacturers often use multi-stage aging processes that optimize both strength and fatigue resistance - critical for components experiencing thousands of flight cycles.
High-Strength Polymers: The Quiet Revolution in Materials Science
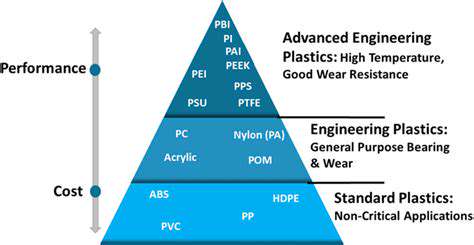
The Molecular Engineering Behind Polymer Strength
Modern high-strength polymers represent a triumph of molecular engineering. Unlike their conventional counterparts, these advanced materials achieve strength through:
- Precisely controlled polymer chain alignment
- Strategic cross-linking at the molecular level
- Nanoscale reinforcement with fibers or particles
The most advanced polymers now rival steel in tensile strength while being 80% lighter. For example, ultra-high-molecular-weight polyethylene (UHMWPE) fibers like Dyneema® demonstrate 15 times the strength-to-weight ratio of steel.
Real-World Applications Changing Industries
These polymers are transforming product design across sectors:
Industry | Application | Benefit |
---|---|---|
Medical | Orthopedic implants | Wear resistance 3x better than metal |
Energy | Wind turbine blades | 50% weight reduction vs. fiberglass |
Defense | Ballistic protection | Stops bullets at half the weight of Kevlar® |
In automotive applications, polymer composites reduce component weight by 30-50% versus metal alternatives, directly improving fuel efficiency and range for electric vehicles.
The Sustainable Future of Advanced Materials
Recent breakthroughs in polymer science are addressing environmental concerns:
- Bio-based nylons from castor oil reduce fossil fuel dependence by 40%
- Chemical recycling technologies can now recover 95% of polymer material
- Self-healing polymers extend product lifespans by 300%
The next decade will see plant-based polymers achieving performance parity with petroleum-based versions, creating truly sustainable high-performance materials. Researchers at MIT recently demonstrated a fully biodegradable polymer with mechanical properties matching ABS plastic.
The Materials Revolution: What's Coming Next
Smart Materials: The Next Frontier
Emerging materials combine structural properties with functionality:
- Self-healing composites that repair microcracks automatically
- Phase-change materials for thermal management in batteries
- Electroactive polymers for shape-changing structures
These innovations will enable adaptive vehicle chassis that optimize aerodynamics in real-time, potentially improving efficiency by 15-20%.
The Sustainability Imperative
Material science is responding to environmental challenges with:
- Closed-loop recycling systems for aluminum with 95% energy savings
- Carbon-negative production methods for polymers
- Bio-based material alternatives reaching commercial scale
As transportation evolves, these advanced materials will play a crucial role in creating vehicles that are lighter, stronger, and more sustainable than ever before.