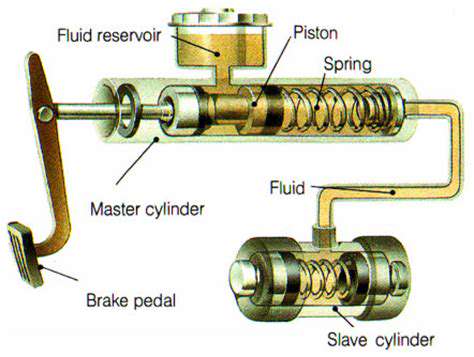
Understanding the Basic Components
The brake master cylinder serves as the heart of your vehicle's braking system. This hydraulic pump transforms the mechanical force from your foot on the pedal into the hydraulic pressure that operates your brakes. As you press the pedal, it activates a piston inside the cylinder, forcing brake fluid through the lines to each wheel's brake assembly. This ingenious mechanical-to-hydraulic conversion is what makes modern braking systems so effective and reliable.
Inside every master cylinder, you'll find precision-engineered components working in harmony. The primary piston moves when you press the brake pedal, while secondary pistons ensure balanced pressure distribution. These components must maintain perfect seals to prevent pressure loss - even microscopic leaks can dramatically reduce braking performance.
The Hydraulic Pressure Transfer Process
Your foot's pressure on the brake pedal initiates a precisely calibrated sequence of events. The pedal's leverage multiplies your force before transferring it to the master cylinder's piston. This piston displacement compresses the brake fluid, creating hydraulic pressure that travels instantaneously through the brake lines. What's remarkable is how this system maintains consistent pressure throughout, ensuring all wheels brake simultaneously with equal force.
Hydraulic fluid's incompressibility makes it ideal for brake systems. Unlike air, which would compress and create delays, hydraulic fluid transmits force immediately and efficiently. This characteristic allows for responsive braking where milliseconds matter, especially in emergency situations where quick stopping could prevent accidents.
The Critical Role of Brake Fluid
Modern brake fluids are engineering marvels, specially formulated to perform under extreme conditions. These synthetic fluids must maintain consistent viscosity whether your brakes are cold or operating at temperatures exceeding 400°F during hard braking. Their high boiling points prevent vapor lock - a dangerous condition where overheated fluid turns to gas and causes brake failure.
Brake fluid also serves as a protective agent for your braking system's metal components. High-quality fluids contain additives that prevent corrosion in the master cylinder, calipers, and steel brake lines. However, these protective properties degrade over time, making regular fluid changes essential for maintaining both performance and component longevity.
Troubleshooting and Maintenance Essentials
Vigilant brake maintenance begins with simple visual inspections. Check your master cylinder reservoir for proper fluid levels and clarity - fresh brake fluid should appear nearly transparent. Dark or cloudy fluid indicates contamination and requires immediate attention. Never ignore a brake warning light or unusual pedal feel, as these often signal developing problems before they become dangerous.
Modern brake systems incorporate multiple redundancy features for safety. Most vehicles have dual-circuit designs that maintain partial braking capability if one circuit fails. Understanding these safety features helps drivers recognize when their system needs professional attention versus when temporary reduced performance might still be safe for cautious driving to a repair facility.
The Importance of Brake Fluid Quality and Capacity
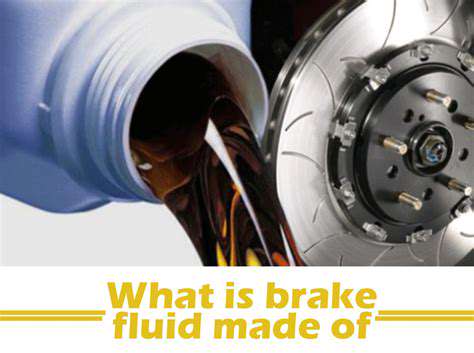
Brake Fluid Viscosity and Temperature Dynamics
Brake fluid viscosity represents a critical balancing act in hydraulic brake systems. Engineers formulate these fluids to flow easily at -40°F while remaining stable at 500°F. This wide operating range ensures reliable braking whether you're starting your car on a frozen morning or descending a steep mountain pass. The fluid's viscosity index - its resistance to thinning when hot and thickening when cold - directly impacts your brake pedal feel and response time.
Seasonal temperature variations present unique challenges for brake fluid performance. In winter, thickened fluid can increase pedal effort, while summer heat may cause premature fluid breakdown. This is why manufacturers specify different fluid grades (DOT 3, 4, 5.1) with varying viscosity characteristics to match climate conditions and driving styles.
Brake Fluid as System Protector
Beyond its hydraulic function, quality brake fluid actively protects your braking system. Modern formulations contain corrosion inhibitors that coat metal surfaces, preventing rust and pitting in critical components. These additives form microscopic protective layers on cylinder walls and piston surfaces, reducing wear and maintaining seal integrity. This protective function becomes increasingly important as manufacturers use more aluminum components in modern brake systems.
Moisture absorption - while inevitable - presents the greatest threat to brake fluid performance. As fluid absorbs water from the air (typically 1-2% annually), its boiling point decreases dramatically. This water contamination can lower boiling points by over 100°F, creating potential safety hazards during aggressive braking. Professional fluid testing with refractometers can accurately measure moisture content before visible symptoms appear.
Maintenance Best Practices
Professional mechanics recommend complete brake fluid replacement every 2-3 years, though severe service (towing, track use, or humid climates) may require annual changes. The flushing process should completely purge old fluid from all circuits, including the often-neglected ABS modulator which can harbor contaminated fluid. Using fresh, sealed fluid containers prevents moisture absorption before installation.
When performing fluid maintenance, technicians often discover other developing issues. Swollen rubber hoses, weeping caliper seals, or corroded fittings frequently become apparent during thorough inspections. Addressing these secondary issues during fluid service prevents future problems and maintains optimal braking performance between scheduled maintenance intervals.
For generations, automotive engineers have refined brake system designs to achieve remarkable reliability. Today's systems combine advanced materials with precision engineering to deliver consistent performance across diverse operating conditions. This evolution continues as emerging technologies like brake-by-wire and regenerative braking systems redefine vehicle stopping dynamics.
Troubleshooting Brake Issues: When the Master Cylinder Fails
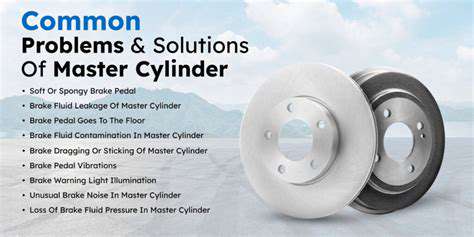
Diagnosing Master Cylinder Problems
Master cylinder failure often manifests through distinct symptoms. A sinking pedal that gradually drops when held under pressure indicates internal seal failure. Fluid leaks around the cylinder body or reservoir confirm external seal issues. These symptoms demand immediate attention as they compromise your entire braking system's functionality.
Diagnostic procedures should include checking for proper pedal free-play (typically 1/4 to 1/2 inch) before resistance begins. Excessive free-play may indicate mechanical linkage problems rather than hydraulic issues. Professional technicians use pressure gauges to measure hydraulic output at each circuit during various pedal applications.
Inspecting Related Brake Components
While diagnosing master cylinder issues, comprehensive mechanics examine the entire system. Brake pad thickness below 3mm warrants replacement, while grooved rotors exceeding manufacturer specifications for runout or thickness variation require resurfacing or replacement. These secondary issues often develop alongside master cylinder problems, compounding braking performance degradation.
Evaluating Fluid Condition and Levels
Brake fluid analysis provides critical diagnostic information. Milky appearance indicates water contamination, while dark fluid suggests thermal breakdown or rubber component deterioration. A sudden fluid level drop points to external leaks, while gradual decrease without visible leaks may indicate worn master cylinder seals bypassing fluid internally.
Complete System Evaluation
Modern ABS-equipped vehicles require specialized diagnostic procedures. Faulty wheel speed sensors or malfunctioning ABS modules can mimic traditional brake problems. Professional shops use manufacturer-specific scan tools to evaluate these complex systems. This level of diagnosis is particularly important when addressing intermittent braking issues that don't follow traditional failure patterns.
Preventative Maintenance Strategies
Proactive maintenance dramatically reduces master cylinder failures. Annual fluid testing, biennial complete flushes, and regular visual inspections catch most developing issues early. When replacing master cylinders, professionals bench-bleed new units before installation to remove trapped air that could compromise initial operation. These meticulous procedures ensure long service life and reliable performance from this critical safety component.