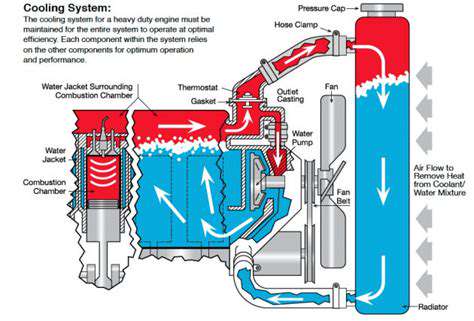
The Importance of Efficient Cooling
Many drivers underestimate the role of engine cooling systems, yet these systems are the backbone of any internal combustion engine's durability. When cooling fails, engines face catastrophic damage—warped pistons, cracked blocks, and seized components become inevitable. Maintaining precise temperature control isn't just about performance; it's about preventing irreversible mechanical trauma.
Excessive heat doesn't merely reduce efficiency—it triggers a domino effect of problems. Power dwindles, fuel consumption spikes, and without intervention, engines reach failure points. Smart vehicle owners recognize that cooling system maintenance isn't optional; it's the difference between a reliable ride and a scrap metal candidate.
Understanding the Components
This thermal regulation network operates through synchronized components. The radiator acts as the system's heat dissipater, while the water pump serves as its circulatory heart. Meanwhile, the thermostat functions as the temperature-sensitive gatekeeper. Remove any one element, and the entire thermal management cascade collapses.
The coolant mixture—typically ethylene glycol blended with water—performs dual duties: heat absorption and corrosion prevention. This chemical cocktail's effectiveness degrades over time, making periodic replacement non-negotiable for responsible vehicle ownership.
The Role of the Radiator
Positioned at the system's front, the radiator exchanges thermal energy between hot coolant and ambient air. Its finned design maximizes surface area for heat transfer. When debris clogs these fins or internal passages corrode, heat dissipation plummets. Radiator maintenance often gets overlooked until temperature gauges spike into danger zones.
The Significance of the Water Pump
This centrifugal pump's impeller creates the hydraulic pressure driving coolant circulation. Modern pumps typically last 60,000-100,000 miles before bearing wear compromises performance. When pump vanes erode or seals fail, coolant flow diminishes—sometimes with no visible symptoms until overheating occurs.
Thermostat Functionality
This temperature-sensitive valve remains closed during cold starts, accelerating warm-up. Once engines reach operating temperature (typically 195-220°F), the thermostat modulates coolant flow to maintain thermal equilibrium. Stuck thermostats—whether open or closed—disrupt this delicate balance with potentially expensive consequences.
Coolant Maintenance and its Importance
Modern coolants contain sophisticated additive packages preventing scale formation and electrolytic corrosion. Using incorrect coolant formulations can silently destroy aluminum components through galvanic corrosion. Manufacturer-recommended change intervals exist for good reason—depleted additives become worse than no protection at all.
Preventive Maintenance for a Healthy Cooling System
Seasoned mechanics recommend biannual cooling system inspections. This includes pressure testing, hose condition evaluation, and coolant pH testing. Proactive maintenance catches minor issues before they escalate into engine rebuild scenarios. Documented service records often correlate directly with engine longevity statistics.
The Mechanics of Coolant Circulation: A Closer Look
Understanding the Closed-Loop System
Pressurized coolant systems operate between 12-18 psi, raising the boiling point approximately 3°F per psi. This engineering prevents vapor lock during extreme conditions. The expansion tank accommodates thermal expansion while maintaining system pressure—a critical function often misunderstood by DIY mechanics.
Coolant follows a precise path: water pump → engine block → cylinder heads → thermostat → radiator → repeat. This circuit ensures even heat distribution while preventing localized hot spots that could warp critical components.
The Vital Role of the Water Pump
Centrifugal pump designs dominate automotive applications due to their simplicity and reliability. The impeller's curved vanes create vortex flow patterns that maintain consistent pressure. When bearing play exceeds 0.5mm or shaft seals leak, pump replacement becomes urgent—not optional.
Coolant Flow Through the Engine Block
Engine designers incorporate specialized coolant jackets around cylinders and combustion chambers. These passages prioritize cooling where temperatures peak during combustion. Blockages in these narrow passages—from sediment or corrosion—create dangerous thermal gradients that stress engine castings.
The Radiator's Role in Cooling
Modern radiators employ parallel-flow designs with aluminum cores and plastic tanks. Their efficiency depends on unobstructed airflow—something compromised by bent fins or debris accumulation. Professional radiator shops measure thermal performance using infrared thermography during diagnostic procedures.
The Importance of Pressure and Expansion Tanks
Pressurization serves multiple purposes: preventing coolant loss through boiling, increasing heat transfer efficiency, and minimizing aeration. The expansion tank's design allows for air separation while maintaining system volume. Faulty pressure caps—often overlooked—account for numerous cooling system failures annually.
Troubleshooting Coolant Circulation Issues
Diagnosing flow problems requires systematic analysis. Technicians use flow meters, pressure differential tests, and thermal imaging to pinpoint restrictions. Common culprits include collapsed hoses, mineral deposits, and failing water pump impellers—each requiring distinct repair approaches.
Maintaining Optimal Engine Temperature
ECUs constantly monitor coolant temperature via multiple sensors, adjusting fuel maps and ignition timing accordingly. Chronic under-temperature operation causes excessive wear through fuel contamination of oil, while overheating risks immediate mechanical failure.
Oncology's digital revolution leverages machine learning to decode complex tumor profiles, while predictive algorithms transform inventory management across medical supply networks.
Signs of a Failing Water Pump: Recognizing the Symptoms
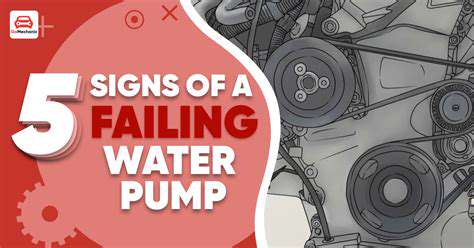
Identifying the Initial Warning Signs
Water pumps rarely fail catastrophically without warning. Early symptoms often manifest subtly—a faint whine during cold starts, minor coolant seepage at the weep hole, or slightly elevated operating temperatures. Mechanics report that 80% of pump failures show detectable symptoms weeks or months before complete breakdown.
Unusual Noises and Vibrations
Bearing failures produce distinctive acoustic signatures. Early stages generate high-frequency whines, progressing to grinding as races pit. Severe cases create palpable vibrations measurable with accelerometers—sometimes exceeding 0.5 inches per second in velocity.
Decreased Water Pressure
Impeller erosion reduces hydraulic efficiency gradually. Technicians quantify this using coolant flow meters, with >15% reduction from specifications indicating necessary replacement. Drivers might notice slightly longer warm-up times or marginal AC performance degradation first.
Leaking or Dripping Water
Modern mechanical seals incorporate multiple lip designs and spring-loaded faces. When these fail, coolant escapes through designated weep holes—an intentional design feature preventing catastrophic failure. Weep hole leakage exceeding 1 drop per minute warrants immediate attention.
Overheating
Localized overheating near the pump often indicates flow restrictions. Infrared thermography reveals temperature differentials exceeding 30°F between pump inlet and outlet during failure conditions.
Slow or Intermittent Operation
Electronically controlled pumps may exhibit PWM signal issues before mechanical failure. Diagnostic scanners can monitor actual versus commanded pump speeds—discrepancies exceeding 10% suggest control or mechanical problems.
Frequent Cycling or Running Time
Pressure switch miscalibration causes abnormal cycling patterns. Data loggers help identify these issues by recording cycle frequency versus system demand. Professional diagnostic equipment can detect problems invisible to casual observation.
Maintaining Your Water Pump for Optimal Performance
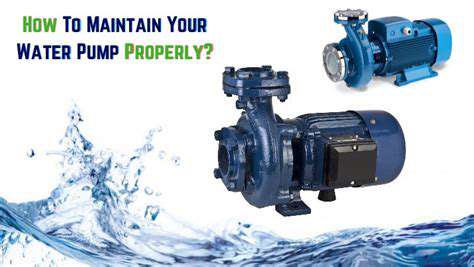
Regular Maintenance
Preventive maintenance schedules vary by pump type—some require annual bearing repacking while others feature lubed-for-life designs. Manufacturer specifications always trump generic advice—consult your service manual for precise intervals.
Cleaning and Flushing
Coolant flush procedures have evolved significantly. Modern reverse-flushing equipment removes up to 98% of contaminants compared to 60-70% with traditional methods. Chemical cleaning agents must match your system's metallurgy—aluminum components require pH-balanced solutions.
Inspecting the Motor
Three-phase motor diagnostics involve checking winding resistance (should balance within 2%), insulation resistance (>1 megohm), and bearing noise (<70dB). Advanced motor analyzers predict failure months in advance by detecting subtle electrical imbalances.
Checking the Impeller and Shaft
Magnetic base dial indicators measure shaft runout—acceptable limits typically fall below 0.003 inches. Impeller clearance checks require feeler gauges, with specifications varying by pump design. Wear beyond 10% of original dimensions usually mandates replacement.
Maintaining the Electrical System
Voltage imbalance between phases shouldn't exceed 1%. Power quality analyzers detect harmonic distortion—above 5% THD accelerates motor winding degradation. Proper torque on electrical connections prevents hot spots that cause intermittent failures.