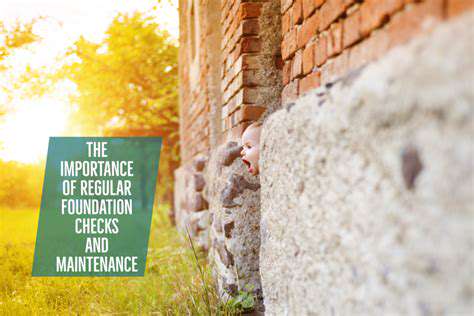
Regular Maintenance: A Proactive Approach
Consistent inspections, frequently neglected, form the bedrock of successful preventative care. Through systematic evaluation of your systems, potential problems can be spotted before they develop into expensive fixes or total system breakdowns. This forward-thinking method reduces operational interruptions and enhances productivity.
Anticipatory maintenance, rooted in routine evaluations, not only protects your investments but also dramatically lowers the chance of sudden malfunctions. Such strategic planning proves essential for sustaining peak performance and decreasing costly operational pauses over time.
Frequency and Scope of Checks
The timing and breadth of these evaluations will differ based on the particular system or machinery. Key considerations involve the equipment type, its working environment, and any past maintenance records. Thorough documentation of these inspections, including dates, observations, and corrective measures, proves vital for monitoring performance and spotting patterns.
Systematic evaluations should include a complete assessment of the equipment's operation, covering mechanical parts, electrical systems, and other critical elements. This guarantees each component works at its best and catches possible concerns early.
Tools and Technologies for Enhanced Checks
Utilizing cutting-edge tools and methods can substantially improve the quality of routine inspections. This incorporates employing advanced diagnostic devices to uncover subtle problems that might otherwise escape notice. Applying data analysis to monitor performance trends and forecast potential issues grows increasingly valuable.
Implementing remote tracking systems enables immediate data gathering and interpretation, allowing quick identification of irregularities and rapid response. This strategy reduces operational pauses and maximizes system availability.
Personnel Training and Expertise
Proper education and knowledge are fundamental for conducting precise and comprehensive routine checks. Staff involved in these evaluations should obtain thorough instruction on specific equipment and protocols, including correct diagnostic tool usage. This guarantees accurate execution of inspections, lowering mistake risks.
Documentation and Reporting
Detailed record-keeping proves indispensable for efficient maintenance management. Complete logs of all inspections, including dates, findings, and required actions, should be meticulously preserved. This data proves priceless for future problem-solving, performance review, and regulatory adherence. Comprehensive records help monitor system history and detect potential patterns or recurring concerns.
Budgeting and Resource Allocation
Establishing a strong preventative maintenance program demands careful financial planning and resource distribution. Allocating adequate funds for necessary tools, training, and personnel to perform routine checks effectively is crucial. Proper budgeting and resource distribution ensure program sustainability and deliver lasting benefits.
Refrigerant Maintenance and Safety
Refrigerant Charge Levels
Keeping proper refrigerant levels in your vehicle's cooling system is vital. Insufficient refrigerant won't cool efficiently, while excessive amounts may damage the compressor. Precision-calibrated instruments are necessary for accurate refrigerant adjustments. This requires specialized tools to measure system pressure and temperature. Improper tool usage can cause serious complications and potentially invalidate warranties.
Periodic refrigerant level verification, particularly after major repairs or noticeable cooling reduction, maintains optimal function and prolongs system life. Ignoring low refrigerant leads to decreased efficiency and higher energy use.
Compressor Health
The compressor serves as the core of your vehicle's cooling system. A failing compressor greatly affects cooling effectiveness and may cause leaks. Listening for abnormal operational sounds like grinding or squealing helps detect potential issues. These noises often signal internal wear needing prompt professional attention.
Routine overheating checks, including visible leaks or excessive compressor heat, help prevent further damage. Immediate diagnosis and repair of compressor problems are crucial for maintaining safe, functional cooling systems.
Leak Detection and Repair
Refrigerant leaks commonly reduce cooling capacity. Locating leak sources is essential for effective repairs. Specialized detection equipment like refrigerant tracers or pressure gauges precisely identifies leak locations. This typically involves careful examination of hoses, connections, and components for visible damage or fluid traces.
Timely leak resolution prevents further refrigerant loss and ensures efficient system operation. Ignoring leaks leads to reduced cooling, increased energy use, and potentially expensive future repairs. Proper sealing techniques prevent recurrence and ensure long-term system reliability.
Proper Disposal of Refrigerant
Correct disposal of used refrigerant is critical for environmental protection. Refrigerants contain harmful chemicals contributing to ozone depletion and climate change if improperly handled. Disposal should always be performed by certified professionals with proper equipment and expertise. Local environmental regulations may specify disposal procedures requiring strict compliance.
Safety Precautions During Maintenance
Safety must remain paramount during refrigerant maintenance. Working with refrigerants involves potentially hazardous substances. Always wear appropriate protective gear including gloves, eye protection, and respirators to minimize exposure risk. Ensure adequate ventilation to prevent fume accumulation.
Understanding and strictly following safety protocols prevents accidents and maintains safe working conditions. Never attempt refrigerant work without proper training and equipment, and consult qualified technicians for any uncertainties.
Regular Maintenance Schedule
Implementing a consistent maintenance schedule significantly enhances long-term cooling system performance. This should include periodic refrigerant level checks, compressor function evaluation, and leak inspections. Routine examinations enable early problem detection, preventing expensive repairs and optimizing efficiency. Regular maintenance also reduces energy consumption and improves driving comfort.
Professional servicing extends system lifespan and ensures peak performance. This proactive approach saves money long-term while protecting the environment by preventing unnecessary refrigerant emissions.
The Importance of Regular Maintenance
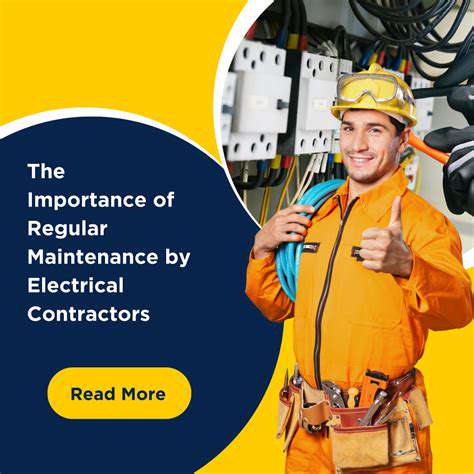
Preventive Maintenance Strategies
Routine maintenance extends beyond problem resolution to proactive prevention. Implementing structured preventive schedules enables early issue identification before they become costly repairs or system failures. This anticipatory method reduces operational pauses and extends equipment lifespan. Addressing minor concerns promptly prevents major operational disruptions.
Effective preventive programs include detailed equipment-specific checklists and schedules considering usage frequency, environmental factors, and wear patterns. Consistent adherence ensures optimal equipment condition and prevents unexpected malfunctions.
Impact on Equipment Lifespan
Consistent maintenance substantially extends equipment longevity. Addressing minor concerns before escalation significantly reduces premature wear risk. Regular care preserves component integrity, ensuring prolonged optimal function. This directly reduces replacement costs and overall operational expenses.
Well-maintained equipment experiences fewer breakdowns, preventing productivity losses. Maintenance investments yield long-term reliability and efficiency benefits, minimizing failure likelihood and saving time and money.
Cost Savings and Efficiency Gains
While maintenance requires initial investment, long-term savings often prove substantial. Preventing breakdowns and expensive repairs dramatically reduces maintenance costs. Preventive care eliminates emergency repairs and unplanned downtime. This boosts productivity and operational efficiency.
Properly maintained equipment operates more efficiently with lower energy consumption. Long-term savings significantly exceed preventive maintenance costs. Regular maintenance investments contribute directly to business success and profitability.
Minimizing Downtime
Operational pauses concern all organizations. Regular maintenance reduces unexpected breakdown risk that causes extended downtime and productivity loss. Proactive issue resolution substantially decreases interruption frequency and duration. Robust preventive programs minimize equipment failure impacts.
Proactive maintenance involves regular inspections, timely part replacement, and early problem resolution. This ensures equipment readiness, minimizes workflow disruptions, and maximizes efficiency.
Enhanced Safety and Compliance
Regular maintenance ensures employee safety and regulatory compliance. Well-maintained equipment malfunctions less, reducing accident and injury risks. Routine inspections identify potential hazards and prevent accidents. This protects workers and prevents legal liabilities.
Strict maintenance adherence ensures equipment meets safety standards. This safety-focused approach demonstrates operational excellence commitment and maintains high workplace safety standards.
Improved Operational Reliability
Consistent maintenance significantly enhances operational dependability. Prompt issue resolution prevents unexpected failures and ensures proper equipment function. This yields more predictable, consistent performance. Well-structured maintenance programs boost overall operational reliability.
Reliable operations increase output, reduce delays, and improve customer satisfaction. Steady, predictable performance is fundamental to operational excellence. This builds positive reputation and strengthens client/partner trust.