Material Selection and Recycling Initiatives
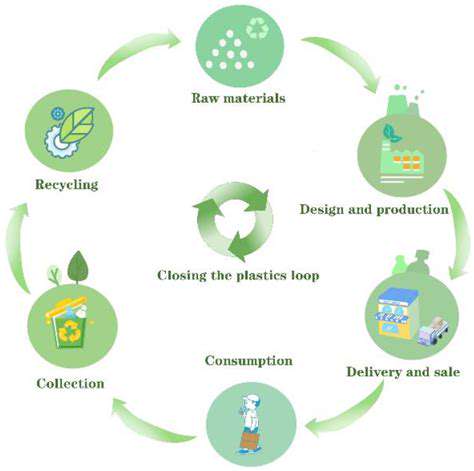
Material Selection Criteria
Selecting the optimal material for any product requires balancing performance, cost, and environmental considerations. Durability, tensile strength, and resistance to degradation must be thoroughly evaluated to ensure extended product lifespans. Modern selection protocols increasingly incorporate sustainability metrics, including recyclability percentages and cradle-to-gate environmental impact assessments. This comprehensive methodology guarantees responsible stewardship throughout a product's entire lifecycle.
Material properties vary dramatically across different substance classes. While polymer-based materials offer exceptional versatility and weight advantages, they frequently lack the structural integrity of metallic alternatives. Metallic components, though exhibiting superior load-bearing characteristics, often entail greater production costs and substantially higher energy expenditures during manufacturing phases.
Metal Recycling Methodologies
Industrial metal recycling represents a critical strategy for minimizing manufacturing's ecological footprint. Standard procedures involve scrap collection, electromagnetic separation by alloy type, followed by high-temperature smelting and purification processes. These techniques dramatically reduce reliance on virgin ore extraction, simultaneously conserving natural resources and slashing energy requirements by up to 75% compared to primary metal production.
Recycling protocols differ substantially between metal families. Aluminum maintains nearly 100% recyclability with negligible property degradation across multiple melting cycles. Ferrous metal recovery, particularly steel, constitutes a major feedstock source for contemporary steelmaking operations globally.
Polymer Recycling Complexities
Post-consumer plastic recycling presents unique technical hurdles due to material diversity and frequent contamination issues. Effective reprocessing demands meticulous resin identification (typically through infrared spectroscopy) and rigorous cleaning protocols to ensure recycled polymers meet application-specific performance standards.
Recycling Implementation Barriers
Despite clear environmental benefits, multiple obstacles impede universal recycling adoption. Contaminant infiltration remains a persistent quality control challenge, often rendering entire batches unsuitable for high-value applications. Advanced sorting technologies and standardized handling procedures prove essential for maintaining material purity and process efficiency.
Inadequate collection infrastructure and misaligned economic incentives continue hampering recycling rates in developing markets. Establishing comprehensive material recovery networks and implementing extended producer responsibility schemes could dramatically improve participation across all sectors.
Economic Implications of Recycling
Material recovery systems generate substantial economic value through multiple channels. The recycling sector creates 10-15 times more employment opportunities than equivalent landfill operations while reducing raw material procurement costs by 30-60%. These operational efficiencies frequently translate into measurable consumer savings for products containing recycled content. Municipalities additionally benefit from reduced waste management expenditures and extended landfill operational lifespans.
Environmental Considerations in Material Specification
Contemporary material selection processes must rigorously evaluate ecological impacts across entire value chains. Prioritizing post-industrial recycled materials and bio-based alternatives can reduce product carbon footprints by 40-70%. Eliminating hazardous substances and selecting materials with favorable end-of-life characteristics proves critical for sustainable manufacturing practices.
Implementing these sustainable material strategies fosters circular economic models that maximize resource utilization while minimizing environmental degradation. Such approaches not only conserve finite resources but also create resilient, future-proof manufacturing ecosystems.
The Circular Economy Framework for Vehicle Lifecycle Management
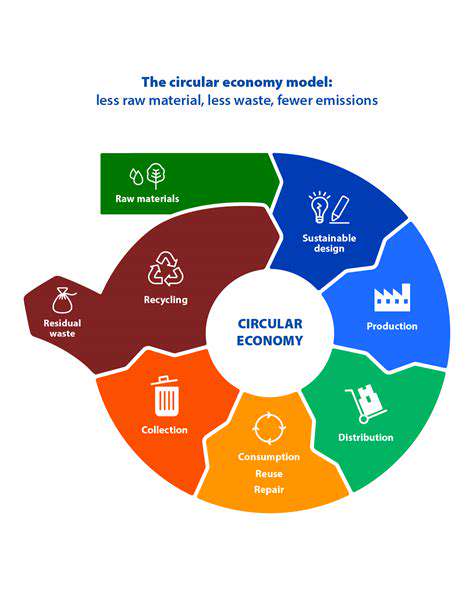
Circular Economy Fundamentals in Automotive Applications
The circular economic model represents a paradigm shift from traditional linear production models to closed-loop material flows. Rather than following the extract-produce-discard sequence, this framework emphasizes continuous resource utilization through strategic reuse, refurbishment, and material recovery. This systemic approach maintains materials in productive use for maximum duration, simultaneously reducing environmental impacts while extracting optimal value from all input resources.
Lifecycle thinking forms the cornerstone of circular vehicle design. Engineers must consider all product phases - from material sourcing through end-of-life processing - while designing for future disassembly and material recovery. This requires fundamental redesign of traditional engineering approaches to prioritize circularity metrics alongside conventional performance criteria.
Material Circularity in Automotive Systems
Implementing circular principles in vehicle manufacturing demands radical material innovation. Designers must specify materials with demonstrated recyclability, engineer components for simplified disassembly, and progressively increase recycled content percentages. Such strategies can reduce vehicle production emissions by 25-40% while decreasing material costs through secondary material markets.
By embracing material circularity, automakers achieve both environmental and competitive advantages. This dual benefit drives innovation while generating 15-30% material cost savings through reduced virgin material dependence. The economic implications become particularly significant at production scale.
Designing Vehicles for Circularity
Vehicle architecture plays a decisive role in circular economy implementation. Modular designs with standardized fasteners and accessible service points dramatically improve repairability and component reuse potential. Strategic material selection for critical components can extend service lives by 50-100% while maintaining or improving performance characteristics.
Multi-Stakeholder Collaboration Models
Successful circular vehicle ecosystems require unprecedented collaboration across value chains. Manufacturers must develop circular design competencies, consumers need access to repair networks, policymakers should implement favorable regulatory frameworks, and researchers must advance material science innovations. Only through coordinated action can the automotive sector achieve meaningful circular transformation.