Precise Material Delivery and Handling
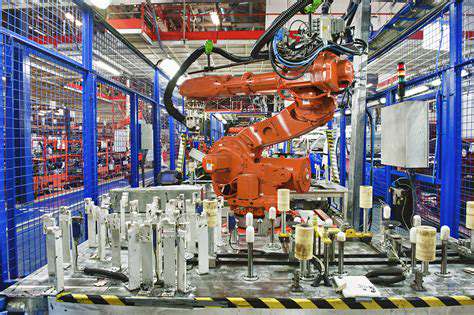
Precise Material Delivery
Material delivery precision plays a pivotal role across diverse sectors including manufacturing, construction, pharmaceuticals, and electronics. Ensuring correct materials arrive in proper quantities at specified locations exactly when needed helps reduce waste, boost efficiency, and cut costs significantly. Achieving this requires meticulous planning, logistics expertise, and cutting-edge tracking technologies that monitor materials throughout their journey.
Optimizing material delivery processes creates a streamlined supply chain essential for thriving in today's competitive business landscape. Accurate demand forecasting, inventory control systems, and efficient transportation networks form the backbone of effective material delivery, all contributing to a company's profitability and market position.
Hand-Based Material Handling
Manual material handling continues to play a crucial role in many operations, particularly for small businesses or specialized applications. Mastering manual techniques—including proper lifting methods, ergonomic considerations, and safety measures—is vital for protecting worker health and preventing workplace injuries. Additionally, understanding material characteristics and specific handling requirements helps maintain product quality and minimize damage.
Effective manual handling typically demands specialized training and equipment to reduce risks while maintaining productivity. Providing workers with appropriate knowledge and tools ensures materials are handled safely and efficiently, preventing accidents and fostering a safer work environment. Comprehensive training in correct lifting procedures remains particularly important.
Advanced Material Handling Systems
Modern material handling solutions represent a quantum leap in operational efficiency. These systems frequently incorporate automation, robotic technology, and intelligent software to refine processes, increase throughput, and decrease human errors. Data analytics integration enables real-time monitoring, process optimization, and predictive maintenance, further boosting operational effectiveness.
Automated handling systems typically deliver superior precision and consistency in material movement. This heightened accuracy results in better quality control and reduced material waste, making these systems worthwhile investments for businesses aiming to refine their operations. They also enhance safety by limiting direct worker contact with heavy or dangerous materials.
Integrating Delivery and Handling
Combining precise material delivery with both manual and automated handling methods yields optimal operational results. Successful integration requires thorough understanding of the complete process chain—from initial procurement and inventory control through to final placement. Cross-departmental coordination and clear communication ensure smooth transitions and minimal workflow interruptions.
A unified strategy that harmonizes delivery and handling methods creates a more efficient operation that reduces disruptions while maximizing productivity. Focusing on these interconnected elements helps businesses develop more resilient supply chains capable of adapting to changing market conditions and unexpected challenges.
Automated Excavation and Grading
Autonomous Excavation: Revolutionizing Site Preparation
Self-operating excavation systems are dramatically changing construction site preparation methodologies. Incorporating robotics and artificial intelligence, these systems perform digging operations with remarkable precision and efficiency, substantially cutting both time requirements and labor costs. Beyond efficiency gains, automation reduces human error potential, enhancing worksite safety. The capacity to navigate complex terrain and diverse soil conditions makes autonomous excavators versatile solutions for various construction projects.
Precision excavation ensures accurate grading—a critical factor for establishing stable foundations. This precision minimizes rework requirements, resulting in long-term cost reductions that underscore the economic advantages of this technology. Automating these tasks allows construction firms to allocate resources to other project priorities, improving overall operational efficiency.
Grading Accuracy and Efficiency
Automated grading systems achieve unparalleled accuracy in land shaping operations. GPS and laser technology integration enables precise measurement and contouring, ensuring final grades meet exact project specifications. This accuracy reduces manual adjustment needs and rework, dramatically improving grading process efficiency. These systems can dynamically adapt to changing terrain conditions, further increasing their effectiveness across different project requirements.
The productivity gains from automated grading are considerable. Reduced human involvement allows faster task completion compared to traditional methods, accelerating project timelines and lowering overall costs. Continuous monitoring capabilities enhance quality control, producing more reliable final results.
Safety Enhancements in Excavation and Grading
Autonomous excavation and grading systems offer substantial safety improvements by removing personnel from hazardous operations. These systems eliminate risks associated with operator fatigue, mistakes, or environmental factors. Robotic operation ensures consistent, error-free task execution, creating safer work environments for all site personnel.
Built-in monitoring and safety features enable proactive hazard identification and prevention. Collected data helps spot potential dangers early, allowing preventive measures to be implemented. This forward-looking safety approach reduces accident risks while promoting a stronger safety culture within the construction sector.
Integration with Other Autonomous Systems
Future construction sites will likely feature extensive integration between various autonomous systems. Excavators and graders can work seamlessly with autonomous loaders and haulers, creating fully automated construction workflows. This integration optimizes the entire process from site preparation through material transportation, dramatically improving project efficiency.
System collaboration enables optimal resource allocation and real-time adaptation to changing conditions. This connectivity enhances construction speed and precision, facilitating completion of more complex projects with greater efficiency and safety.
Cost-Effectiveness and ROI
While initial investments in autonomous excavation systems appear significant, the long-term financial benefits prove substantial. Reduced labor expenses, minimized rework, faster project completion, and improved safety all contribute to strong returns on investment. These systems also decrease reliance on manual labor, generating savings on wages and overtime costs.
Reduced operational downtime further enhances cost-effectiveness. Minimizing delays and disruptions creates more predictable project timelines, saving both time and resources. Combined, these factors demonstrate compelling ROI for companies adopting this technology.
Future Trends and Developments
Autonomous excavation technology continues evolving with promising advancements in artificial intelligence, machine learning, and sensor systems. Future systems will likely feature enhanced sensors for better environmental awareness and more intuitive control interfaces. Potential integration with emerging construction technologies—such as 3D printing and BIM—could further transform industry practices, enabling more efficient and sustainable construction methods.
Automated Inspection and Maintenance
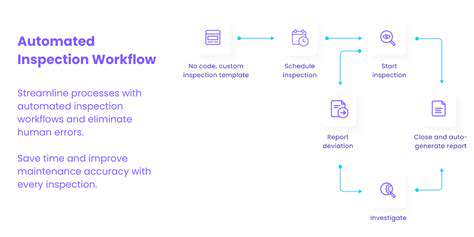
Automated Inspection Systems
Automated quality inspection systems are transforming multiple industries by providing faster, more accurate defect detection. These solutions employ computer vision, machine learning, and integrated sensors to analyze products and processes. Automation dramatically reduces dependence on manual inspection, decreasing human error while improving efficiency. Rapid processing of large data volumes enables quick anomaly detection and corrective action implementation.
Implementation often leads to substantial quality improvements. Early defect identification prevents expensive rework, product recalls, and customer dissatisfaction. Collected data can reveal trends enabling process optimization and workflow improvements. Benefits extend beyond quality control to include enhanced safety protocols and reduced equipment downtime.
Maintenance Prediction and Scheduling
Predictive maintenance strategies optimize equipment lifespan while minimizing unplanned outages. Advanced sensors and analytical tools monitor equipment condition continuously, enabling early fault detection and proactive maintenance. Predictive approaches outperform reactive maintenance in cost efficiency, safety improvement, and operational effectiveness.
Analysis of historical data, performance metrics, and environmental factors enables accurate maintenance scheduling, preventing unexpected failures and maximizing uptime. This methodical approach avoids costly emergency repairs and production interruptions.
Benefits extend beyond downtime reduction. Performance trend analysis provides valuable insights for equipment design, operation, and maintenance procedure improvements. This data-driven methodology fosters continuous organizational improvement and optimization.
Predictive maintenance significantly reduces costs associated with unplanned downtime by minimizing emergency repairs and optimizing maintenance schedules—a critical advantage in competitive markets that ensures efficient resource allocation.
Integration and Data Management
Successful automated inspection and maintenance require effective system integration and data management. Connecting inspection systems with maintenance software and operational databases provides comprehensive equipment performance visibility, enabling better decision-making. System integration creates seamless workflows that optimize productivity while minimizing resource waste.
Effective data management is essential for deriving meaningful insights from automated systems. Robust data storage, processing, and analysis capabilities identify patterns leading to efficiency improvements and cost reductions. Large-scale data analysis enables anomaly detection and predictive model development for future maintenance needs.
Specialized Robots for Specific Tasks
Specialized Robots for Excavation
Purpose-built excavation robots are transforming construction site operations. Equipped with sophisticated sensors and precision controls, these machines handle trenching, foundation work, and earthmoving with exceptional accuracy. Their ability to work in confined spaces and perform repetitive tasks with minimal supervision boosts productivity while reducing error risks—particularly important when handling delicate or hazardous materials.
Programmable excavation paths and real-time depth adjustment capabilities ensure optimal results with minimal material waste. These robots reduce heavy machinery requirements and limit human exposure to hazardous conditions, significantly improving site safety.
Automated Material Handling Robots
Automated material transporters are revolutionizing construction material logistics. Utilizing advanced navigation and gripping systems, these robots autonomously move building materials from storage to work areas. Automation reduces physical strain on workers, decreases handling-related injuries, and significantly improves construction efficiency.
Optimized material flow creates more organized, productive workflows that accelerate project completion. Precise material tracking and management through robotic systems enhance inventory control while reducing loss or misplacement incidents.
Construction Inspection and Monitoring Robots
Robotic inspection systems play an increasingly vital role in construction quality control and safety assurance. Equipped with high-resolution imaging and advanced sensors, these robots conduct real-time structural inspections, material quality assessments, and hazard identification. Proactive quality control minimizes costly errors while ensuring compliance with project standards.
Collected data enables prompt identification of improvement areas, allowing managers to implement corrective measures efficiently. This enhances final product quality while creating safer work environments for construction teams.
Robots for Concrete Placement and Finishing
Specialized robotic systems automate concrete pouring and finishing operations. These machines precisely position concrete within forms, creating smooth, consistent surfaces—even in hard-to-reach areas. Automation reduces labor costs, minimizes material waste, and improves concrete work quality.
Robotic concrete systems contribute to more efficient workflows, allowing crews to focus on other critical tasks and accelerating project timelines. Their integration into construction processes significantly impacts concrete work speed and quality.
Specialized Robots for Demolition and Waste Management
Robotic systems are increasingly important for demolition and waste handling operations. Equipped with powerful demolition tools, these robots safely dismantle structures while sorting and compacting waste materials—reducing environmental impact. Their ability to operate in hazardous, confined spaces makes them invaluable for demolition projects.
Robotic demolition reduces worker injury risks while increasing operational efficiency. Automated waste handling promotes more sustainable, environmentally responsible construction practices.