Understanding the Intake Manifold's Function
The intake manifold plays a vital role in an engine's operation, serving as the primary pathway for delivering the air-fuel mixture to the cylinders. Its most important job is ensuring each cylinder receives an equal share of this mixture, which is absolutely necessary for proper combustion. When this distribution works correctly, the engine runs smoothly and delivers its full power potential. Without a well-functioning intake manifold, engines struggle with poor performance and uneven operation.
Engineers pay close attention to manifold design because it dramatically affects how well air moves through the system. The length of the runners, their diameter, and the overall shape all contribute to how efficiently air flows. A bad design can cause cylinders to receive unequal amounts of air, leading to power loss and rough idling. That's why manifold design receives so much attention during engine development and tuning.
Impact on Engine Performance
The intake manifold's quality directly determines how well the engine performs. A properly designed unit helps the engine breathe easily, improving both fuel economy and power output. On the other hand, problems with the manifold can drag down performance, causing noticeable drops in horsepower and making the engine run rougher.
Designers must consider multiple factors when creating intake manifolds. The engine's specific requirements, fuel type, and desired performance characteristics all influence the final design. Getting these elements right means the difference between an average engine and an exceptional one. The connection between manifold design and engine performance remains one of the most important relationships in automotive engineering.
Maintaining and Troubleshooting Intake Manifold Issues
Keeping the intake manifold in good condition requires regular attention. Owners should check for visible damage like cracks or leaks, and watch for dirt buildup that can restrict airflow. Periodic cleaning, especially around the throttle body area, helps maintain proper air movement and prevents performance problems.
When issues arise, diagnosis requires careful observation. Symptoms like rough idling, misfires, or power loss often point to manifold trouble. A skilled technician can pinpoint whether the solution requires cleaning, repair, or complete replacement. Accurate diagnosis saves time and money while restoring the engine to proper operation.
Airflow Dynamics and Manifold Design
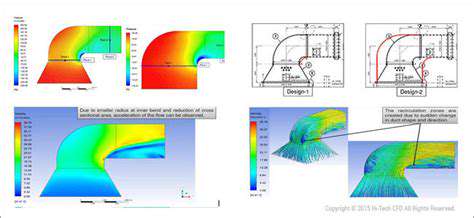
Airflow Characteristics
Effective manifold design begins with understanding airflow behavior. Air speed, pressure changes, and temperature variations all significantly affect system performance. Ignoring these factors can create uneven airflow, reducing efficiency and potentially damaging components. Modern engineers use sophisticated computer simulations to model these effects during development.
Air properties like density and thickness also influence flow patterns, as does the manifold's interior shape. Any obstacles inside the manifold further complicate airflow. Accounting for all these variables ensures the system works efficiently and reliably.
Manifold Geometry and Design
The manifold's physical shape determines how air moves through it. Engineers must carefully design the internal passages to deliver equal air quantities to all cylinders. This involves precise calculations of channel sizes and careful placement of any curves or restrictions.
Different layout approaches - whether parallel, converging or diverging - each affect airflow differently. The best choice depends entirely on the engine's specific needs and operating conditions.
Material Selection and Manufacturing
Material choice significantly impacts manifold performance. The selected material must endure operating pressures and temperatures while resisting wear. In harsh environments, corrosion resistance becomes especially important to prevent premature failure.
Precision manufacturing ensures the final product matches the design specifications exactly. Smooth internal surfaces and accurate dimensions are critical for proper airflow. Poor craftsmanship can introduce problems that undermine the entire design.
Computational Fluid Dynamics (CFD) Analysis
Modern design relies heavily on computer simulations. These powerful tools let engineers visualize airflow and identify potential issues before building physical prototypes, saving considerable time and development costs.
CFD allows testing different design variations digitally, helping optimize the manifold for specific performance goals. This capability has revolutionized manifold development, leading to more efficient designs.
Testing and Validation
Real-world testing remains essential despite advanced simulations. Measurements of actual airflow, pressure changes, and distribution uniformity verify the design works as intended. This validation process confirms the manifold meets all performance requirements before going into production.
Comparing test results with simulation predictions helps improve future designs, creating a continuous improvement cycle.
Optimization Strategies
Perfecting a manifold design requires balancing multiple factors. Iterative improvements to shape, materials, and production methods combine to achieve peak performance. This optimization considers the complete system requirements - air volume, pressure needs, and operating temperatures.
The best solutions emerge from combining theoretical analysis, computer modeling, and practical testing. This comprehensive approach delivers manifolds that maximize engine efficiency and power.
Impact of Manifold Material and Construction on Performance
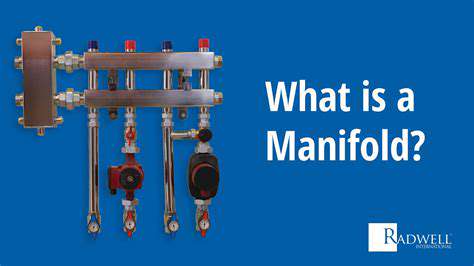
Impact of Manifold Material on Performance
The manifold's construction material directly affects its capabilities. Selecting the appropriate material ensures proper flow characteristics and pressure management. Materials vary in heat transfer properties, corrosion resistance, and strength - all critical for reliable operation. Stainless steel excels in demanding applications because it resists corrosion exceptionally well, while copper works better where heat transfer matters most. Understanding these differences ensures choosing the right material for each application.
Material choice also affects costs. Some high-performance alloys carry premium prices. Smart selection balances upfront costs with long-term reliability and maintenance requirements, ensuring the best value over the product's lifespan.
Co-factors Affecting Manifold Performance
Beyond materials, several other elements influence manifold operation. The design itself - including internal passage shapes and connection points - determines flow patterns and pressure losses. Poor design can create performance bottlenecks or even safety hazards.
The fluid being moved also matters greatly. Different liquids or gases have unique flow characteristics that affect manifold behavior. Accounting for these differences during design prevents operational problems later.
Environmental conditions present another consideration. Extreme temperatures or pressures can degrade materials or cause failures. The manifold must withstand all expected operating conditions without compromise.
Finally, manufacturing quality makes a major difference. Even the best design fails if production standards aren't maintained. Rigorous quality control ensures each manifold meets specifications and performs reliably, especially in critical applications where failures carry serious consequences.