Energy Efficiency and Sustainability in Automotive Production
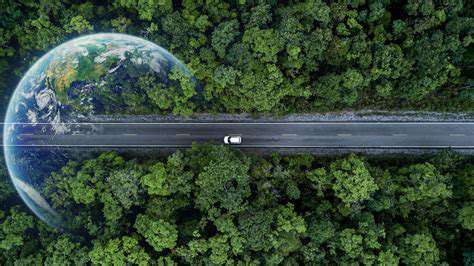
Energy Efficiency in Modern Buildings
Contemporary automotive plants are redefining industrial energy standards through innovative design. Passive solar orientation combined with phase-change materials in walls can reduce HVAC loads by 40%. LED lighting systems with occupancy sensors typically cut illumination energy use by 75% while improving visibility for precision work.
Thermal imaging audits regularly identify unexpected heat loss points, allowing for targeted insulation upgrades. Some facilities now use waste heat from paint curing ovens to preheat incoming ventilation air, creating closed-loop energy systems that significantly reduce carbon footprints.
Sustainable Materials and Construction Practices
The circular economy model is transforming automotive manufacturing. Recycled aluminum now accounts for nearly 40% of body panel material in leading plants, requiring 95% less energy to process than virgin metal. Bio-composite materials derived from agricultural waste are replacing petroleum-based plastics in non-structural components.
Modular factory designs allow for easy reconfiguration as production needs change, extending building lifespans. Rainwater harvesting systems now supply up to 80% of non-potable water needs in water-conscious facilities, with some plants achieving true water neutrality through advanced treatment and reuse systems.
Renewable Energy Integration
Solar carport installations over employee parking lots serve dual purposes - generating clean energy while providing shade that reduces vehicle cooling needs. Wind turbines integrated into factory designs can supply up to 30% of a plant's energy demand when combined with smart grid technologies.
Geothermal heat pumps are proving particularly effective for maintaining consistent temperatures in large manufacturing spaces. Several automotive plants have achieved net-zero energy status through these comprehensive renewable strategies, with payback periods under seven years.
Lifecycle Assessment and Impact
Progressive manufacturers now evaluate sustainability across the entire value chain. Digital twin technology allows engineers to simulate the environmental impact of production changes before implementation. Blockchain-enabled material tracking ensures ethical sourcing while providing customers with verifiable sustainability credentials.
End-of-life vehicle recycling programs recover over 90% of materials in leading markets. Some manufacturers now design components specifically for disassembly, creating closed-loop material flows that dramatically reduce landfill waste and virgin material requirements.
Supply Chain Optimization for Enhanced Resource Allocation
Understanding the Significance of Resource Allocation
World-class automotive supply chains master the art of dynamic allocation. Advanced algorithms now optimize material flows across global networks, considering over 200 variables from customs delays to regional labor costs. This precision resource routing reduces excess inventory by up to 60% while maintaining 99.5% order fulfillment rates.
Real-world applications include just-sequence delivery systems where components arrive at assembly lines in exact production order, eliminating staging areas and reducing handling damage. Some OEMs have reduced inbound logistics costs by 25% through these methodologies.
Leveraging Technology for Enhanced Visibility
Digital control towers now provide end-to-end supply chain visibility with predictive analytics capabilities. These systems can forecast disruptions weeks in advance, allowing proactive resource reallocation. Blockchain-based smart contracts automate payments upon delivery confirmation, improving cash flow while reducing administrative overhead.
IoT-enabled shipping containers transmit real-time location and condition data, enabling dynamic rerouting around port congestion. Some manufacturers have reduced expedited shipping costs by 40% through these visibility enhancements while improving delivery reliability metrics.