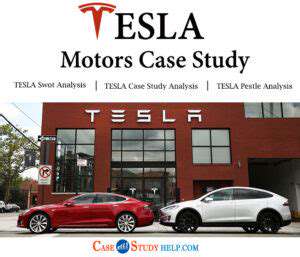
Tesla's Vision for Sustainable Manufacturing
When you walk into one of Tesla's massive Gigafactories, the first thing that strikes you is how differently they approach manufacturing. Unlike traditional auto plants belching smoke, these facilities hum with clean energy. What really sets them apart is their obsession with squeezing every ounce of efficiency from renewable sources while eliminating waste at every turn. Their secret sauce? An unrelenting focus on reimagining every step of production through an eco-conscious lens.
The factories themselves are marvels of sustainable architecture. Massive solar arrays blanket the roofs, while innovative water recycling systems cut consumption by staggering amounts. It's not just about looking green - these facilities prove that environmental responsibility can go hand-in-hand with cutting-edge manufacturing. Workers move through brightly lit spaces where natural lighting reduces energy needs, showing that sustainability impacts everything from the ground up.
Gigafactory's Impact on Battery Technology
Inside these factories, the real magic happens at the battery production lines. The scale of operations here has single-handedly transformed the economics of battery production. Where others see obstacles, Tesla's engineers see opportunities - constantly finding ways to shave cents off production costs while boosting performance. This relentless optimization has made their batteries both cheaper and better, a rare combination in manufacturing.
I spoke with one engineer who explained how they've reworked the battery chemistry itself to use less cobalt while improving energy density. These aren't incremental changes - they're complete reimaginings of how batteries work, enabled by the factory's massive production capacity that allows for constant experimentation.
Operational Efficiency and Supply Chain Management
What fascinates industry observers most is how Tesla has rewritten the rules of automotive supply chains. By bringing everything under one roof - from raw materials to finished batteries - they've cut out layers of inefficiency that plague traditional manufacturers. Where competitors wait weeks for parts shipments, Tesla moves materials between production stages in hours.
The logistics are staggering to behold. Automated guided vehicles zip materials precisely where needed, while real-time data analytics predict and prevent bottlenecks before they occur. This isn't just efficient - it's a masterclass in industrial choreography, with every movement carefully orchestrated to eliminate waste.
Economic Impact and Job Creation
The ripple effects of these factories extend far beyond their walls. Local economies near Gigafactories have transformed almost overnight, with new businesses springing up to support the thousands of well-paying jobs created. I met several workers who relocated hundreds of miles for these opportunities, drawn by the chance to work on cutting-edge technology.
More impressive than the initial construction boom is the lasting impact. These facilities act as magnets for talent and investment, creating entire ecosystems of suppliers and service providers that elevate entire regions. The economic transformation is so profound that competing manufacturers are now scrambling to replicate Tesla's model.
Challenges and Future Considerations
Of course, nothing this ambitious happens without hurdles. The most fascinating challenge? Scaling their workforce as fast as they scale production. Training thousands of workers on highly specialized equipment requires innovative approaches to workforce development that could reshape manufacturing education nationwide.
Looking ahead, the factories themselves will need to evolve. The next generation of Gigafactories will likely integrate even more renewable energy sources and closed-loop recycling systems. As battery technology advances, these facilities must remain flexible enough to adopt new processes quickly - a challenge that will test Tesla's innovative spirit to its limits.
Case Study 2: Volkswagen's Commitment to Renewable Energy in Production Facilities
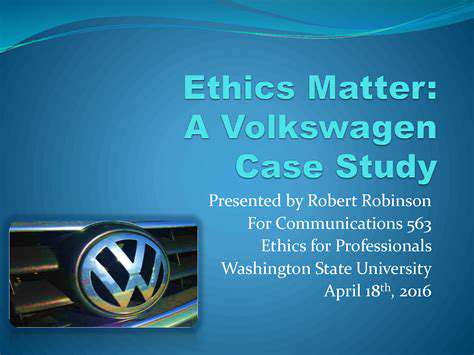
Volkswagen's Commitment to Sustainability
Walking through Volkswagen's transformed factories, it's clear this isn't your grandfather's automaker anymore. The company has undertaken one of the most ambitious corporate sustainability transformations in history, and the changes are visible everywhere. From solar-powered assembly lines to zero-waste initiatives, they're proving that even industrial giants can reinvent themselves for the green economy.
Addressing Emissions and Fuel Efficiency
What's most impressive is how they've attacked emissions from multiple angles. While competitors focus solely on tailpipe emissions, Volkswagen's engineers have scrutinized every aspect of production - even the paint booths now use revolutionary low-emission processes. The result? Facilities that produce vehicles with dramatically smaller carbon footprints from start to finish.
The Rise of Electric Vehicles
Their electric vehicle push represents more than just new models - it's a complete rethinking of manufacturing. The ID. series production lines demonstrate how electric vehicles demand entirely different factory layouts and processes. Battery assembly areas resemble tech clean rooms more than traditional auto plants, reflecting the precision required for EV manufacturing.
Supply Chain Sustainability
Perhaps their boldest move has been extending sustainability requirements to suppliers. Now, getting a contract with Volkswagen means meeting strict environmental standards that ripple across the entire supply chain. This creates a powerful multiplier effect, forcing positive change throughout the industry.
Public Perception and Brand Image
The transformation has done wonders for their reputation. Where Volkswagen once evoked emissions scandals, it's increasingly associated with sustainability leadership. Marketing teams wisely highlight their green initiatives, but the real story is in the billions being invested to make these changes substantive rather than superficial.
Financial Implications and Future Outlook
The financial calculus is fascinating. While the upfront costs are enormous, Volkswagen bets that sustainability investments will pay off through regulatory compliance, customer loyalty, and long-term efficiency gains. It's a high-stakes gamble that could redefine how we value environmental responsibility in corporate balance sheets.
The combination of 5G and analytics creates operational efficiencies that were previously unimaginable. Walking through modern factories equipped with these technologies feels like seeing into the future - sensors track every component, predicting maintenance needs before humans notice issues. The potential savings are staggering, but more importantly, these systems enable sustainability by eliminating waste at unprecedented scales.
Beyond Solar and Wind: Exploring Other Renewable Energy Options
Geothermal Energy: Harnessing Earth's Heat
Visiting a geothermal plant reveals an often overlooked renewable gem. Unlike temperamental wind and solar, these facilities provide rock-solid reliability, generating power steadily regardless of weather. The engineering challenges are substantial - drilling deep into the earth's crust isn't simple - but the payoff is a nearly perfect baseload power source.
Hydropower: Tapping into Water's Potential
Modern hydropower facilities have come a long way from their ecological nightmare reputation. The newest designs incorporate fish-friendly turbines and careful water management that minimizes environmental impact while maximizing output. It's a balancing act that, when done right, creates clean energy without devastating local ecosystems.
Biomass Energy: Utilizing Organic Matter
The most innovative biomass plants now look more like high-tech refineries than simple incinerators. Advanced gasification systems can extract energy from agricultural waste with stunning efficiency while producing useful byproducts like biochar. When properly managed, these systems create circular economies where nothing goes to waste.
Marine Energy: Harnessing Ocean Power
Experimental wave and tidal projects hint at an exciting frontier. The raw power of ocean movements dwarfs land-based renewables, but harnessing it requires ingenious engineering solutions. The most promising prototypes use clever buoy systems or underwater kites that dance with the currents to maximize energy capture.
Ocean Thermal Energy Conversion (OTEC): Harvesting Temperature Differences
OTEC represents one of the most elegant energy concepts - using nature's own temperature gradients. Pilot plants in tropical locations prove the concept works, though scaling remains challenging. The potential is enormous for island nations and coastal regions where deep cold water lies conveniently close to shore.
Hydrogen Fuel Cells: A Future Energy Source
The hydrogen economy inches closer to reality with each passing year. What excites engineers most is hydrogen's versatility - it can power everything from cars to steel plants without direct emissions. The remaining hurdles center on creating green hydrogen at scale and building out distribution networks, but the pieces are gradually falling into place.
The Future of Sustainable Automotive Manufacturing: A Collaborative Approach
Decentralized Manufacturing and Supply Chains
The next generation of auto plants may look completely different. Instead of massive centralized factories, we'll see networks of smaller, specialized facilities located near both suppliers and markets. This distributed model slashes transportation emissions while creating manufacturing jobs in more communities. The key will be coordinating these decentralized operations through advanced logistics systems.
Sustainable Materials and Manufacturing Processes
Material science breakthroughs are rewriting manufacturing rules. From mushroom-based interior panels to recycled ocean plastic body components, tomorrow's cars will be grown and forged from surprising sources. The most exciting developments come from cross-industry collaborations - like using aerospace composites in mainstream vehicles.
Renewable Energy Integration
The factories of the future won't just use renewable energy - they'll be designed around it. Smart microgrids will balance solar, wind, and storage to match production schedules with energy availability. Some plants may even become net energy exporters, transforming industrial facilities from power consumers to power providers.
Collaborative Design and Engineering
Sustainable innovation thrives on cross-pollination. We're seeing unprecedented cooperation between automakers, tech firms, and material scientists to solve environmental challenges. Open-source platforms for sustainable manufacturing knowledge are emerging, accelerating progress across the entire industry.
Circular Economy Principles
The endgame is vehicles designed for infinite reuse. Forward-thinking manufacturers are pioneering modular designs where every component can be easily separated, repaired, or recycled. Some even experiment with leasing critical components like batteries, ensuring they're properly recycled while reducing upfront costs.
Government Policies and Incentives
Policy innovations are proving as important as technological ones. The most effective regulations create frameworks that reward sustainability without stifling innovation. Carbon pricing mechanisms and recycled content requirements are gradually aligning economic incentives with environmental goals, creating a virtuous cycle of improvement.